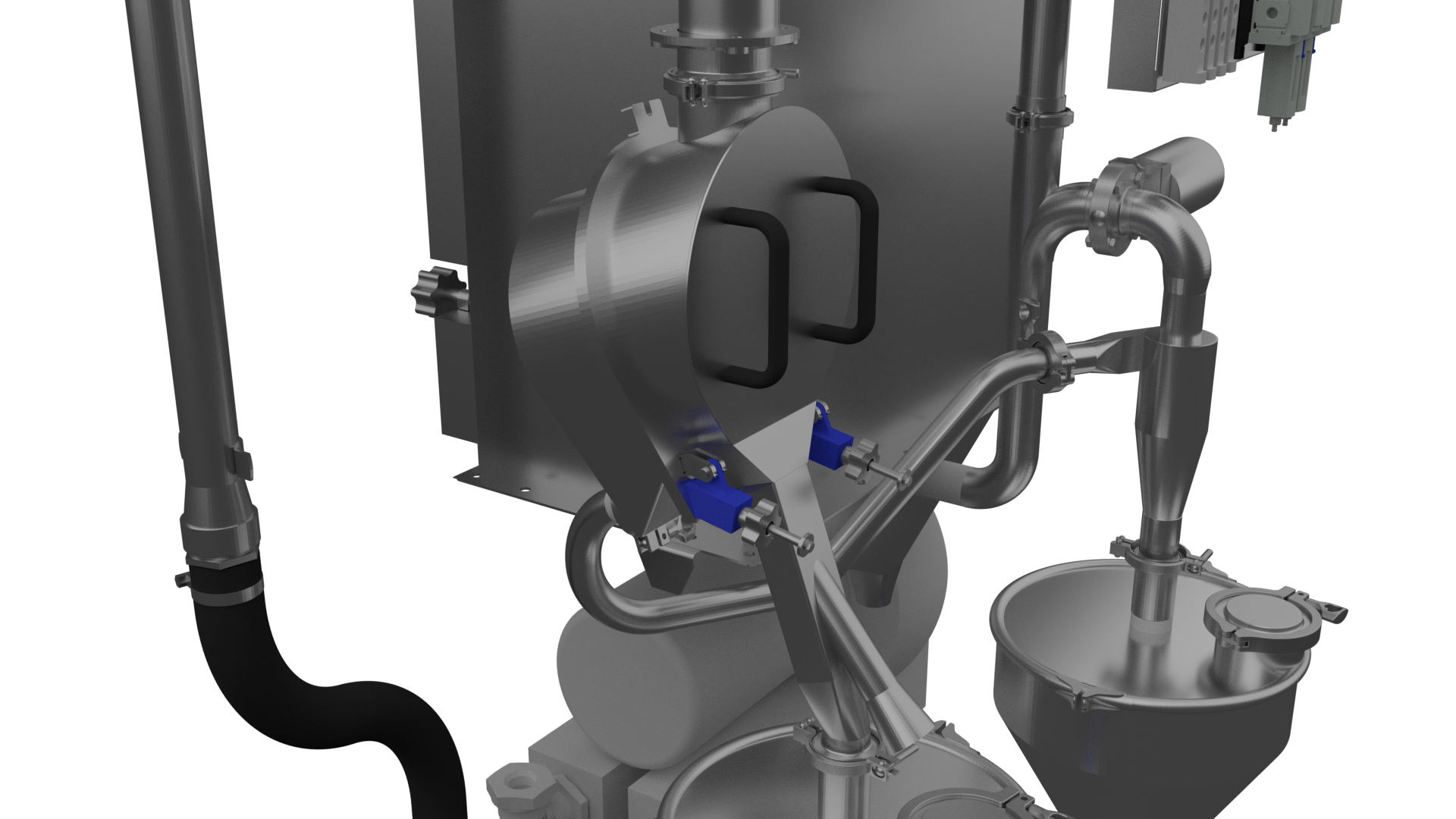
Vacuum sieving
In this phase, the particles within the desired range are efficiently separated from oversized particles using a controlled pressure differential mechanism. Additionally, an innovative wipe blade system, powdered by air pressure, ensures that the sieve remains unobstructed, preventing clogs in the filter. To maintain the optimal sieving process, our automated dosing system dynamically adjusts the powder delivery rate, allowing the sieve ample time to process the material effectively. This integrated approach guarantees a streamlined, uninterrupted operation, ensuring the highest level of material processing efficiency.